Bei der Automatisierung in der Robotik zeichnen wir uns durch Präzisionstechnik aus und entwickeln anpassungsfähige Robotersysteme, die auf verschiedene Anwendungen zugeschnitten sind. Unsere Expertise umfasst die Rationalisierung betrieblicher Prozesse, die Sicherstellung gleichbleibend hochwertiger Ergebnisse und die Entwicklung innovativer Lösungen für die vorausschauende Wartung. Wir konzentrieren uns auf die Verbesserung der Mensch-Roboter-Zusammenarbeit und die Revolutionierung industrieller und logistischer Arbeitsabläufe im Hinblick auf Effizienz und Effektivität.
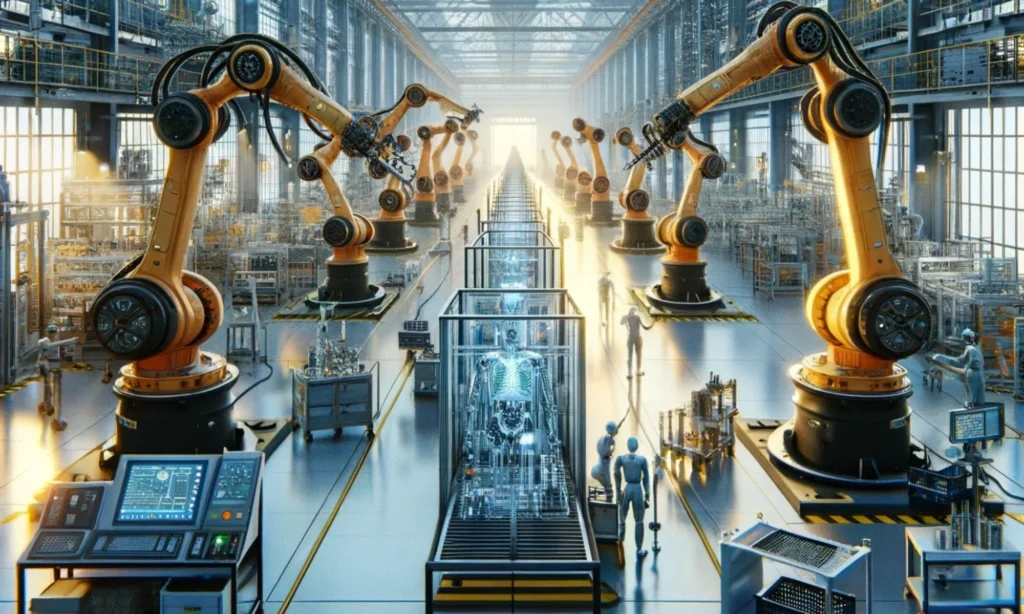
Automatisierung in der Robotik umfasst den Einsatz künstlicher Intelligenz (KI) und Robotertechnologien zur Ausführung von Aufgaben, die traditionell von Menschen erledigt werden. Dieser Bereich gewinnt in modernen Industrien zunehmend an Bedeutung und kann erhebliche Auswirkungen auf Produktivität, Sicherheit und Effizienz haben.
Was ist Automatisierung?
Unter Automatisierung versteht man die Verwendung von Steuerungssystemen zum Betrieb von Geräten, Maschinen und anderen Prozessen mit minimalem oder keinem menschlichen Eingriff. Im Kontext der Robotik geht es darum, Roboter zur Durchführung automatisierter Aufgaben einzusetzen, was zu einer schnelleren Produktion, verbesserter Qualität und geringeren Betriebskosten führen kann. Es ist auch bekannt, dass automatisierte Systeme die Sicherheit verbessern, indem sie gefährliche oder sich wiederholende Aufgaben von Menschen übernehmen.
Was ist Robotik?
Robotik ist ein interdisziplinärer Zweig, der die Konstruktion, den Bau und den Betrieb von Robotern umfasst. Es umfasst Aspekte der Mechatronik, Elektronik und Softwaretechnik. Der Schwerpunkt der Robotik liegt auf der Entwicklung von Maschinen, die auf programmierte Weise mit ihrer Umgebung interagieren können, oft um komplexe oder gefährliche Aufgaben auszuführen.
Automatisierung in der Robotik
Bei der Automatisierung in der Robotik geht es darum, Robotergeräte zur autonomen Ausführung von Aufgaben einzusetzen. Diese Form der Automatisierung ist in verschiedenen Sektoren weit verbreitet, darunter Fertigung, Montage, Inspektion, Wartung und Gesundheitswesen. Das Hauptziel besteht darin, die Produktivität und Effizienz zu steigern und gleichzeitig die Betriebskosten zu senken.
Vorteile der Automatisierung in der Robotik
- Erhöhte Produktivität: Roboter können Aufgaben schneller und genauer ausführen als Menschen, insbesondere bei sich wiederholenden oder präzise arbeitenden Arbeiten.
- Kostensenkung: Automatisierung kann zu erheblichen Arbeitskosteneinsparungen führen und möglicherweise die Materialkosten durch effiziente Ressourcennutzung senken.
- Verbesserte Sicherheit: Roboter können gefährliche Aufgaben ausführen und so das Verletzungsrisiko für menschliche Arbeiter verringern.
- Flexibilität: Roboter können für verschiedene Aufgaben umprogrammiert werden, was Unternehmen betriebliche Flexibilität bietet.
- Verbesserte Qualität: Roboter können Waren mit höherer Konsistenz und weniger Fehlern produzieren und so die Produktqualität insgesamt verbessern.
Nachteile der Automatisierung in der Robotik
- Kosten: Die anfängliche Einrichtung und Wartung automatisierter Systeme kann teuer sein.
- Inflexibilität: Einige automatisierte Systeme haben möglicherweise Schwierigkeiten, sich schnell an Änderungen oder neue Aufgaben anzupassen.
- Schulungsanforderungen: Die effektive Nutzung automatisierter Systeme erfordert häufig eine umfassende Mitarbeiterschulung.
- Sicherheitsbedenken: Wenn automatisierte Systeme nicht ordnungsgemäß konzipiert und implementiert werden, können sie ein Sicherheitsrisiko darstellen.
Zukunft der Automatisierung in der Robotik
Die Zukunft der Automatisierung in der Robotik sieht vielversprechend aus: Entwicklungen wie kollaborative Roboter (Co-Bots), die auf die Zusammenarbeit mit Menschen ausgelegt sind, und Fortschritte bei der KI machen Roboter anpassungsfähiger und intelligenter. Diese Innovationen werden wahrscheinlich weiterhin verschiedene Branchen verändern, indem sie die Effizienz und Fähigkeiten automatisierter Systeme verbessern. Die Rolle der KI, die es Robotern ermöglicht, im Laufe der Zeit zu lernen und sich anzupassen, ist besonders wichtig für die Verbesserung ihrer Effektivität bei komplexen Aufgaben.
Zusammenfassend lässt sich sagen, dass die Automatisierung in der Robotik ein sich schnell entwickelndes Feld mit erheblichen Auswirkungen auf die Zukunft von Arbeit und Industrie ist. Es bietet viele Vorteile, darunter höhere Effizienz, Kosteneinsparungen und verbesserte Sicherheit, birgt aber auch Herausforderungen wie hohe Anschaffungskosten und die Notwendigkeit spezieller Schulungen. Da die Technologie weiter voranschreitet, wird erwartet, dass sich die Fähigkeiten und Anwendungen der Roboterautomatisierung erweitern und Branchen und Arbeitsabläufe weiter verändern.
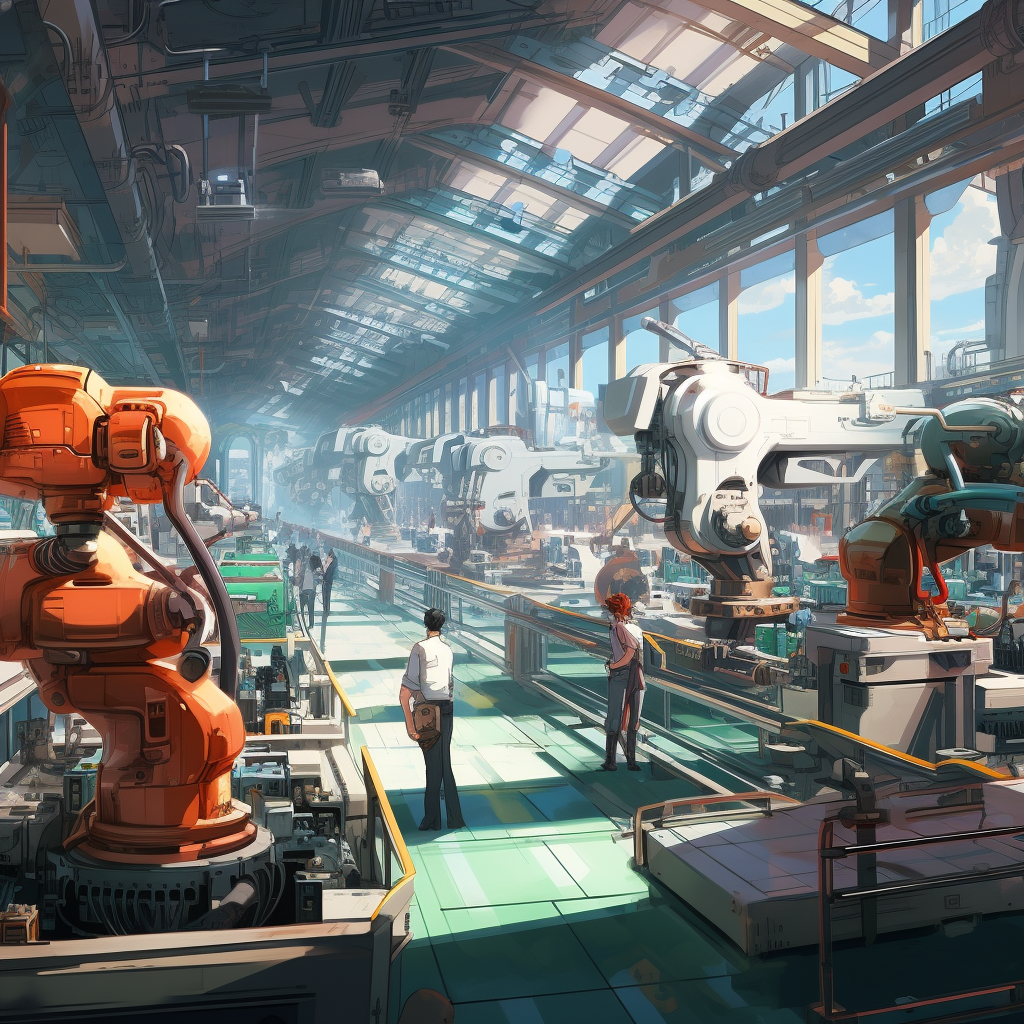
Collaborative Robots (Cobots) in Manufacturing
Exploring how cobots are designed to work alongside humans in the production line, enhancing efficiency and safety
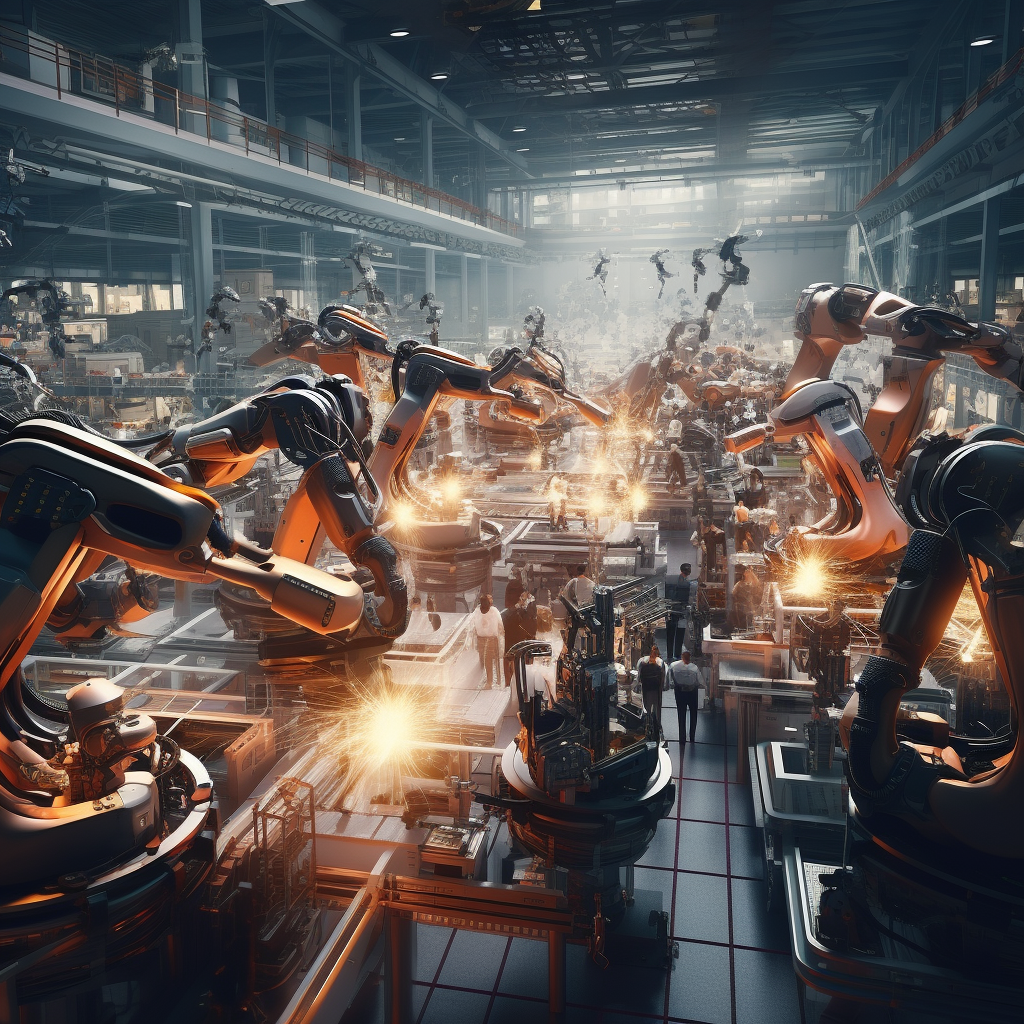
Automation in Quality Control
Investigating the role of advanced robotics and AI in improving quality control processes in manufacturing, including visual inspection and defect detection
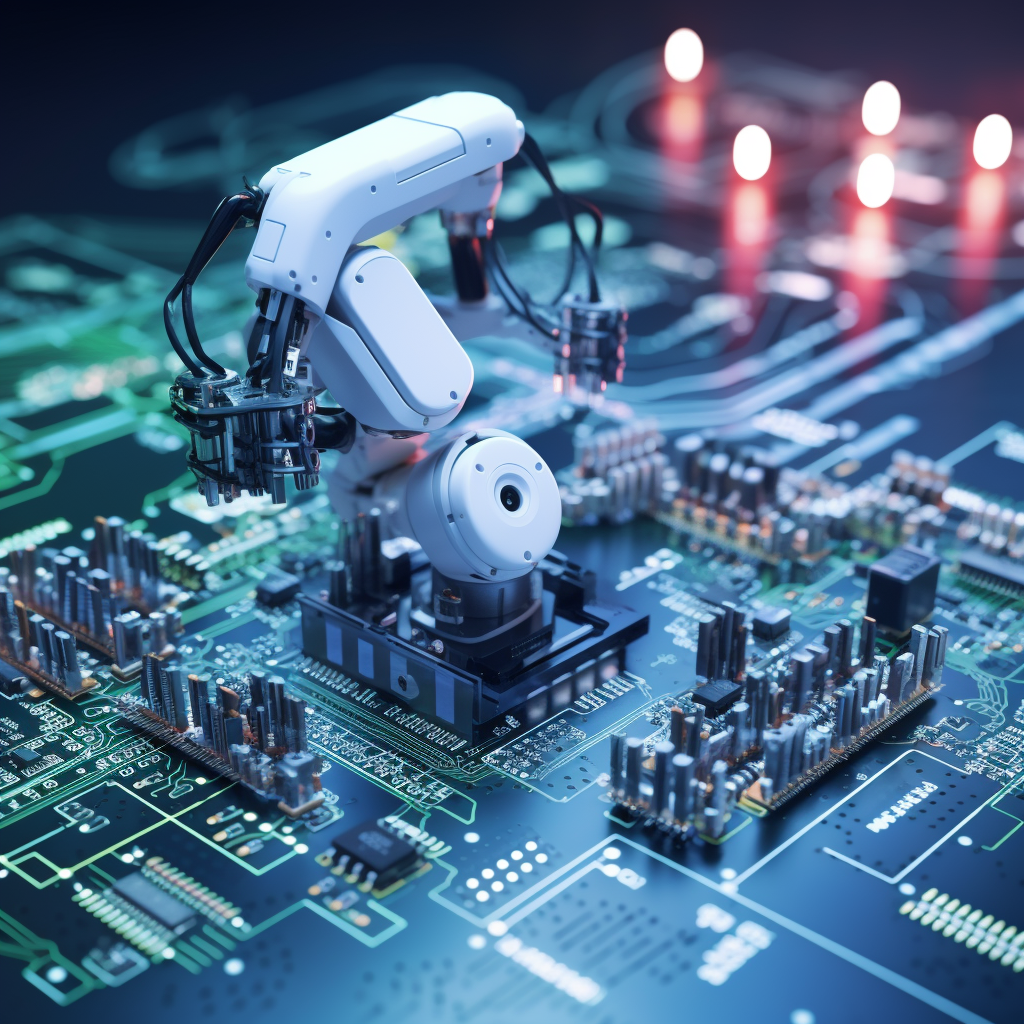
Autonomous Material Handling Robots
Studying the impact of self-guiding robots in logistics and material handling within production facilities, including their integration with warehouse management systems.
Collaborative Robots, often referred to as cobots, represent a significant shift in the landscape of industrial automation. These devices are designed to work alongside human workers, complementing their capabilities and enhancing productivity and safety. As of 2023, the field of collaborative robotics is witnessing exciting innovations and developments, indicating robust growth and expansion across various industries.
Cost and Accessibility
Cobots are generally more affordable than traditional industrial robots, with prices ranging from $7,000 to over $50,000. This pricing is particularly attractive for small to medium-sized businesses that are keen on implementing automation but lack the budget for conventional systems. In comparison, traditional industrial robots can cost anywhere from $25,000 to over $400,000.
Types of Cobots
The categorization of cobots can be based on their mode of operation, among other factors. The main types include:
- Power and Force Limiting Cobots: These are designed for shared workspaces with humans. They have embedded sensors to detect abnormal forces and halt operations to prevent injury.
- Safety Monitored Stop Cobots: These cobots stop functioning when an object comes within a certain distance and resume once the object is cleared. They are less comprehensive in safety features but offer faster cycle times.
- Speed and Separation Cobots: Also known as “fenceless” systems, they adjust their speed based on human proximity, slowing down or stopping as humans get closer.
- Hand Guiding Cobots: These cobots learn through direct human input and are easily reprogrammable, making them versatile for various tasks.
Innovations in 2023
Several new models of cobots have emerged in 2023, each with unique features:
- JAKA Robotics: These cobots are 5G enabled and can be controlled by any smart device, eliminating the need for a proprietary pendant. They are versatile and highly accurate, suitable for a range of tasks including assembly, packaging, and welding.
- IBG’s FC RoboLite: A hybrid of a cobot arm and an automated guided vehicle, designed for heavy-duty logistics tasks.
- Han’s Robot’s Elfin-Pro Series: These cobots are suitable for harsh environments and are even explosion-proof. They are also being explored for use in health applications like automated massage therapy.
- ReBel Cobot by igus: Notable for its affordability and lightweight design, this cobot is ideal for both industrial and educational use.
Future Outlook
The market for collaborative robots is projected to grow substantially in the coming years. A report from Interact Analysis estimates the collaborative robot market to reach $7.5 billion by 2027, constituting about 29% of the global industrial robot market. This growth is fueled by the flexibility, safety, and productivity advantages that cobots offer.
The future of cobots includes continued growth and diversification into various industries. While certain technological barriers still exist, ongoing innovations are driving the industry forward. The market projections suggest that collaborative robots will become increasingly prevalent both inside and outside of traditional factory settings.
In conclusion, collaborative robots are transforming the landscape of industrial automation, offering cost-effective, safe, and flexible solutions for a wide range of applications. Their growth is a testament to their potential in enhancing productivity and operational efficiency in various sectors.
Automation in Quality Control has become a pivotal aspect of modern manufacturing and production processes. This integration of advanced technologies aims to enhance product quality, reduce errors, and streamline operations. The key trends and developments in this area for 2023 include:
- Addressing Labor Shortages: Industries are facing significant labor shortages, particularly in tasks that are considered dull, dirty, or dangerous. Automation in quality control helps fill these labor gaps, improving productivity and consistency in quality.
- No Code and User-Friendly Robotics: Innovations in robotics have led to the development of user-friendly, no-code robots. Companies like Wandelbots, Rapid Robotics, and Ready Robotics have created robots that do not require complex programming, making automation more accessible to small and medium-sized businesses. These robots are increasingly collaborative, flexible, and dexterous, facilitating rapid deployment in various industrial settings.
- Expansion into New Industries: Automation in quality control is no longer confined to traditional manufacturing sectors. It’s now being adopted in industries such as hospitality, construction, agriculture, and healthcare. This trend is driven by the diverse applications of robotics in tasks like food preparation, fruit picking, and hospital logistics.
- Cybersecurity and Sustainability Considerations: With the proliferation of connected robotic systems, cybersecurity has become a critical concern. Companies are tailoring their strategies to protect these systems from cyber threats. Furthermore, the environmental impact of robots and automation technologies is being scrutinized, leading to a focus on sustainability and responsible resource use.
- Growth of Mobile Robots: The rise in e-commerce and the need for efficient logistics have fueled the adoption of mobile robots in warehouses, distribution centers, and healthcare facilities. This sector is expected to continue growing robustly, with predictions of a significant increase in the installed base of mobile robots by 2027.
- Reshoring Initiatives: With increasing labor costs overseas and declining automation costs, there’s a growing trend of reshoring manufacturing activities to the U.S. Automation is key in making these initiatives feasible, helping to shorten supply lines and potentially reducing emissions for more sustainable manufacturing.
These trends highlight the dynamic evolution of quality control automation, underlining its critical role in modern industry. The focus is not only on enhancing efficiency and productivity but also on addressing broader challenges such as labor shortages, cybersecurity risks, and environmental sustainability.
Autonomous Material Handling Robots (AMHRs) are revolutionizing the way materials are handled in various sectors, including manufacturing, warehousing, and logistics. These robots are designed to operate independently, navigating through facilities to transport goods and materials efficiently. The key trends and advancements in this domain for 2023 include:
- Advanced Navigation and Sensing Technologies: Modern AMHRs are equipped with sophisticated sensors and navigation systems, allowing them to move safely and efficiently through complex environments. Technologies such as LiDAR, computer vision, and AI-driven algorithms enable these robots to understand and adapt to their surroundings, avoid obstacles, and optimize routes.
- Increased Collaboration and Flexibility: There is a growing trend towards collaborative robots that can work alongside human workers, enhancing efficiency and safety. These robots are designed to be more adaptable and flexible, capable of performing a variety of tasks and easily reprogrammable for different workflows.
- Integration with IoT and Data Analytics: The integration of AMHRs with the Internet of Things (IoT) and data analytics platforms is becoming more prevalent. This allows for real-time tracking of goods, predictive maintenance of robots, and optimization of material flow based on data-driven insights.
- Scalability and Customization: As businesses seek solutions that can scale with their operations, manufacturers of AMHRs are focusing on offering scalable and customizable solutions. This includes modular designs that can be easily expanded or modified to meet changing business needs.
- Energy Efficiency and Sustainability: With a growing emphasis on sustainability, there is a push towards more energy-efficient and environmentally friendly AMHRs. This includes the use of renewable energy sources, such as battery technologies that are more efficient and have a lower environmental impact.
- Enhanced Safety Features: Safety remains a top priority in the development of AMHRs. This includes advanced safety features such as collision avoidance systems, emergency stop functions, and compliance with rigorous safety standards.
- Application in Diverse Industries: While traditionally used in manufacturing and warehousing, AMHRs are now being deployed in a wider range of industries, including healthcare, retail, and agriculture. This expansion is driven by the versatility and efficiency improvements offered by these robots.
- Remote Monitoring and Control: Advances in connectivity and cloud computing enable remote monitoring and control of AMHRs. This facilitates better management and coordination of robotic fleets, even across multiple locations.
- E-commerce and Last-Mile Delivery: The e-commerce boom has accelerated the adoption of AMHRs, particularly in the context of order fulfillment and last-mile delivery. These robots are increasingly being used to automate the picking, packing, and delivery processes.
- Partnerships and Collaborative Ecosystems: There is a trend towards strategic partnerships between AMHR manufacturers, technology providers, and end-users. This collaborative approach fosters innovation and accelerates the development of more advanced and integrated material handling solutions.
In conclusion, autonomous material handling robots are at the forefront of transforming logistics and manufacturing operations. With their ability to enhance efficiency, safety, and flexibility, they are becoming an integral part of the modern industrial landscape. As technology continues to evolve, we can expect these robots to become even more sophisticated, adaptable, and integral to a wide range of industries.
Robotics in Precision Assembly
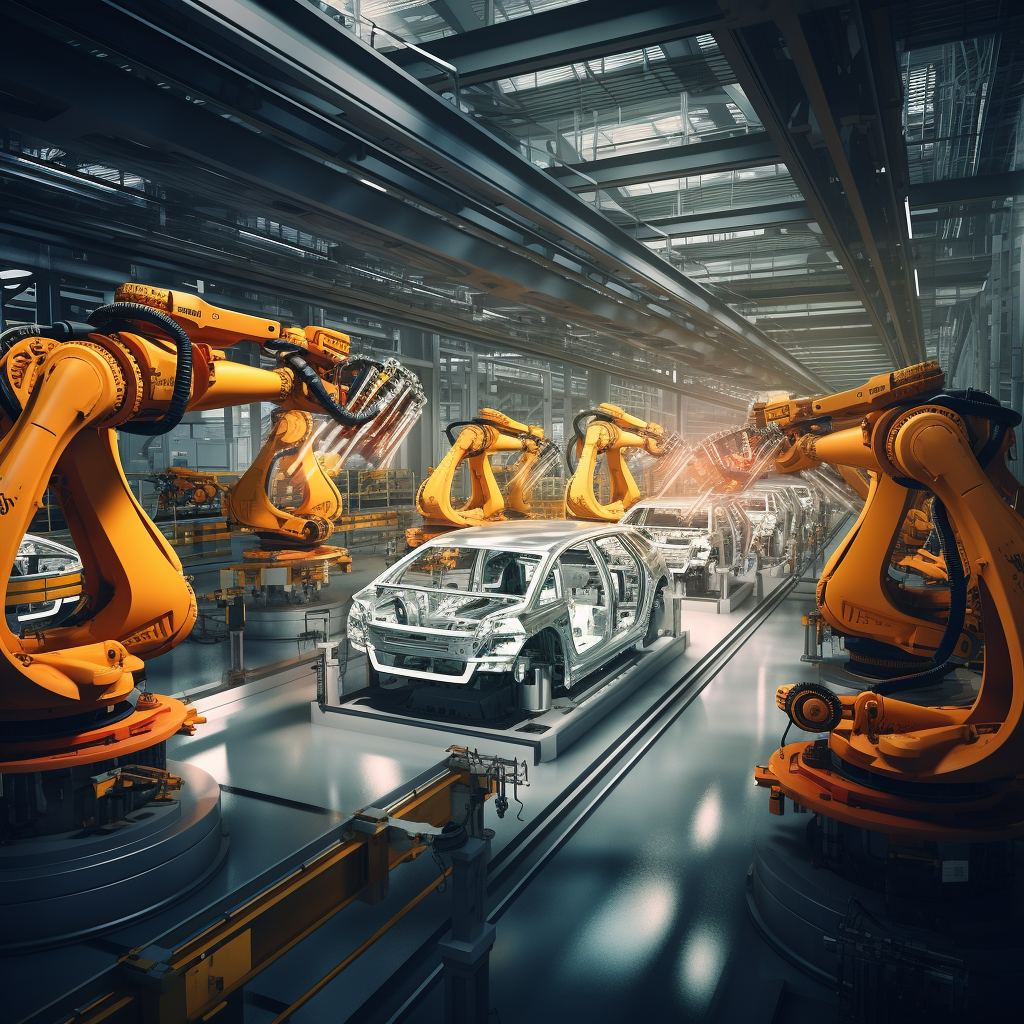
Robotics in precision assembly, particularly in the electronics and automotive manufacturing industries, has seen significant advancements and is characterized by several key features and trends:
- Types of Robots Used in Electronics Manufacturing: The electronics manufacturing industry commonly employs several types of robots, each with specific advantages. These include collaborative robots (cobots), Cartesian robots, SCARA (Selective Compliance Assembly Robot Arm), and six-axis robots. Cobots are popular in electronics manufacturing due to their ability to work closely with humans in tasks that are small, lightweight, and require high precision. Cartesian robots are known for their high precision due to their rigid and straightforward construction, while SCARA robots are chosen for their blend of precision, speed, and reach. Six-axis robots are used in a wide range of applications due to their flexibility and complex motion capabilities.
- High-Speed and Precision: The requirement for high precision is a critical factor in electronics and semiconductor industries, as components are becoming smaller. This necessitates robots with precision gripper designs and the ability to handle higher inertia due to fast process speeds. The use of vision systems and other adaptive tools, such as force control, allows robots to place parts with high accuracy in dynamic assembly processes. The precision of robots is complemented by their ability to perform repetitive tasks thousands of times without noticeable deviation, leading to consistent production quality.
- Shift Towards Delta Robots: In the realm of semiconductor and electronics manufacturing, there is a growing preference for delta-style robots. These robots are suited for high-speed operations and are becoming more popular due to their speed and better accessibility under their work envelopes. Delta robots provide a larger work envelope and have six-axis articulation, making them highly effective for tasks that require parts to be oriented and placed into precise positions.
- Cleanroom Considerations: Many electronics and semiconductor applications require operations in cleanroom environments. This necessitates the use of specially handled and packaged robots that do not introduce contaminants into these sterile fields. Robots used in cleanrooms are often assembled with special lubricants and shipped with protective packaging to maintain their sterile state.
- Collaborative Robots in Precision Applications: Cobots are increasingly becoming the optimal choice for precision applications in industries like electronics, automotive, and aerospace. These robots are known for being lightweight, easy to program, and capable of working in close proximity to human workers. They are particularly effective in tasks that are categorized as „dull, dirty, or dangerous“ for humans, making them ideal for automation in precision applications. Their ability to be easily reprogrammed and redeployed makes them highly versatile and efficient in various precision tasks.
In summary, the use of robotics in precision assembly within the electronics and automotive industries is driven by the need for high precision, speed, and the ability to perform repetitive tasks with consistency. The adoption of various types of robots, including cobots and delta robots, is tailored to meet the specific requirements of precision assembly tasks in these industries. The shift towards automation with robotics in these sectors is enhancing operational efficiency, production quality, and the ability to work in specialized environments like cleanrooms.
AI-Driven Predictive Maintenance in Manufacturing
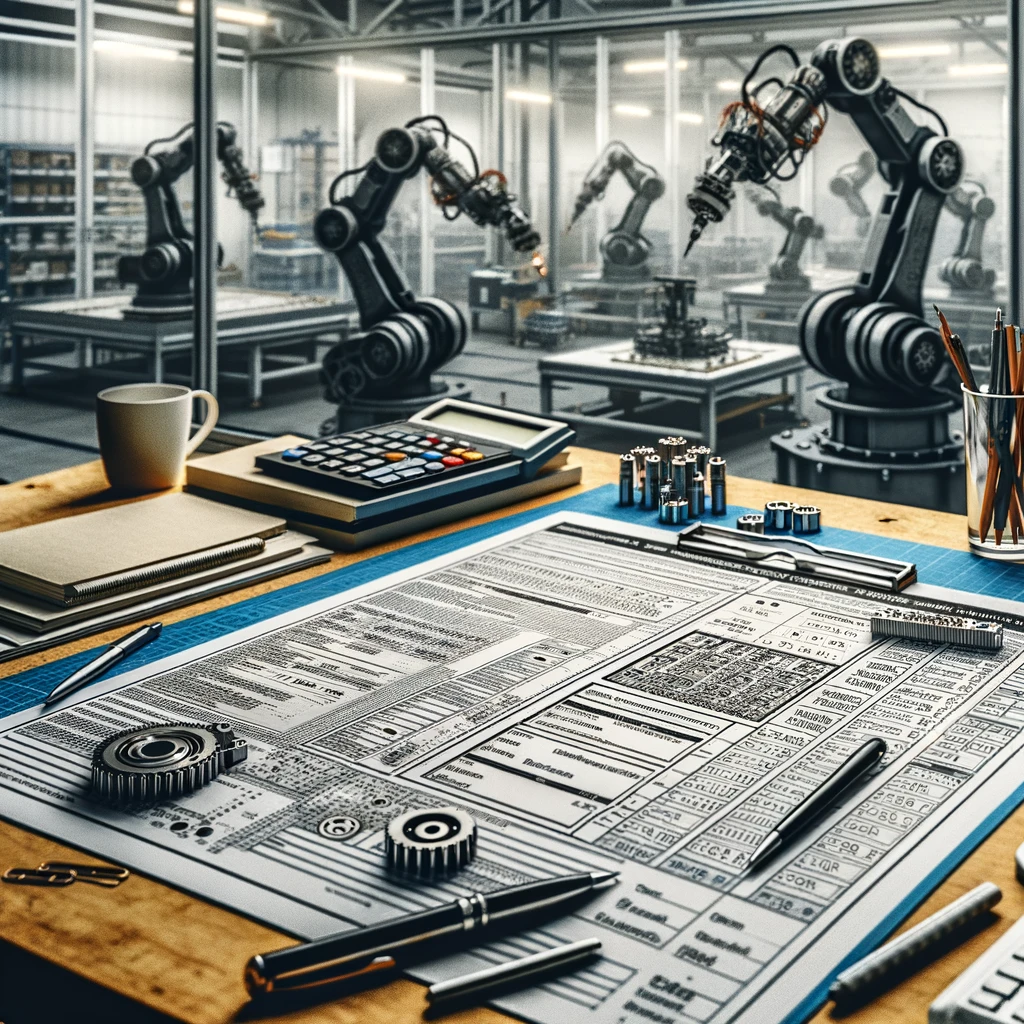
AI-driven predictive maintenance in manufacturing is a rapidly evolving field, characterized by the integration of cutting-edge technologies and methodologies to enhance operational efficiency and reliability. The key trends in this area for 2023 and beyond include:
- Artificial Intelligence and Machine Learning: Industries are increasingly leveraging AI and ML for analyzing massive volumes of real-time data to predict asset breakdowns. This involves collecting data from in-machine sensors and past service records to inform operators about components needing maintenance or replacement, thereby reducing costs associated with unscheduled maintenance and ensuring worker safety.
- Internet of Things (IoT): IoT plays a crucial role in predictive maintenance, enabling manufacturers to connect and monitor assets centrally. Smart sensors provide real-time information crucial for forecasting machine failures and mitigating downtimes. This results in more efficient use of machines, improved safety, and optimized production processes
- Inspection Technologies: Systematic condition monitoring is integral to predictive maintenance. Technologies such as infrared thermography, ultrasonic analysis, vibration monitoring, and robotic inspection are used for non-invasive and cost-effective testing of equipment. The combination of these methods accurately indicates probable sources of deterioration, improving asset reliability
- Digital Twins: Digital twin technology, creating virtual replicas of physical equipment, is becoming increasingly important. It enables continuous monitoring of actual working conditions and visualization of future scenarios. Manufacturers can use digital twins to predict anomalies and problematic areas that might cause equipment failure, thereby improving decision-making and maintenance strategies
- Predictive Analytics: Predictive maintenance solutions use analytics to analyze unstructured data, such as sensor readings and environmental parameters, to predict equipment failures. Big data platforms improve system health transparency and enable precise modeling and effective forecasting
- Predictive Maintenance as a Service (PMaaS): PMaaS is making predictive maintenance more accessible and affordable for manufacturers. Cloud-based PdMaaS solutions reduce infrastructure costs and allow on-demand access to predictive maintenance, improving scalability and eliminating the need for significant infrastructure and development costs
- Immersive Technologies: Extended reality technologies, like augmented reality (AR) and virtual reality (VR), are simplifying asset inspections. Technicians can use AR to collect data from equipment sensors to support predictive maintenance planning, enhancing on-the-spot visualization and early fault detection
- Synergizing with ERP Systems: Integrating predictive maintenance with Enterprise Resource Planning systems has become vital, allowing real-time insights for optimizing maintenance plans, reducing unscheduled downtime, and enhancing operational efficiency
- Economic Advantage and Third-Party Partnerships: By embracing PMaaS and collaborating with third-party providers, manufacturers can achieve significant cost savings, focus on their core competencies, and benefit from advanced maintenance capabilities
In summary, these advancements in AI-driven predictive maintenance are not only enhancing operational efficiencies and reducing downtime in manufacturing but are also paving the way for smarter, more connected, and sustainable manufacturing practices. As these technologies continue to evolve, they offer significant potential for revolutionizing industrial maintenance strategies.